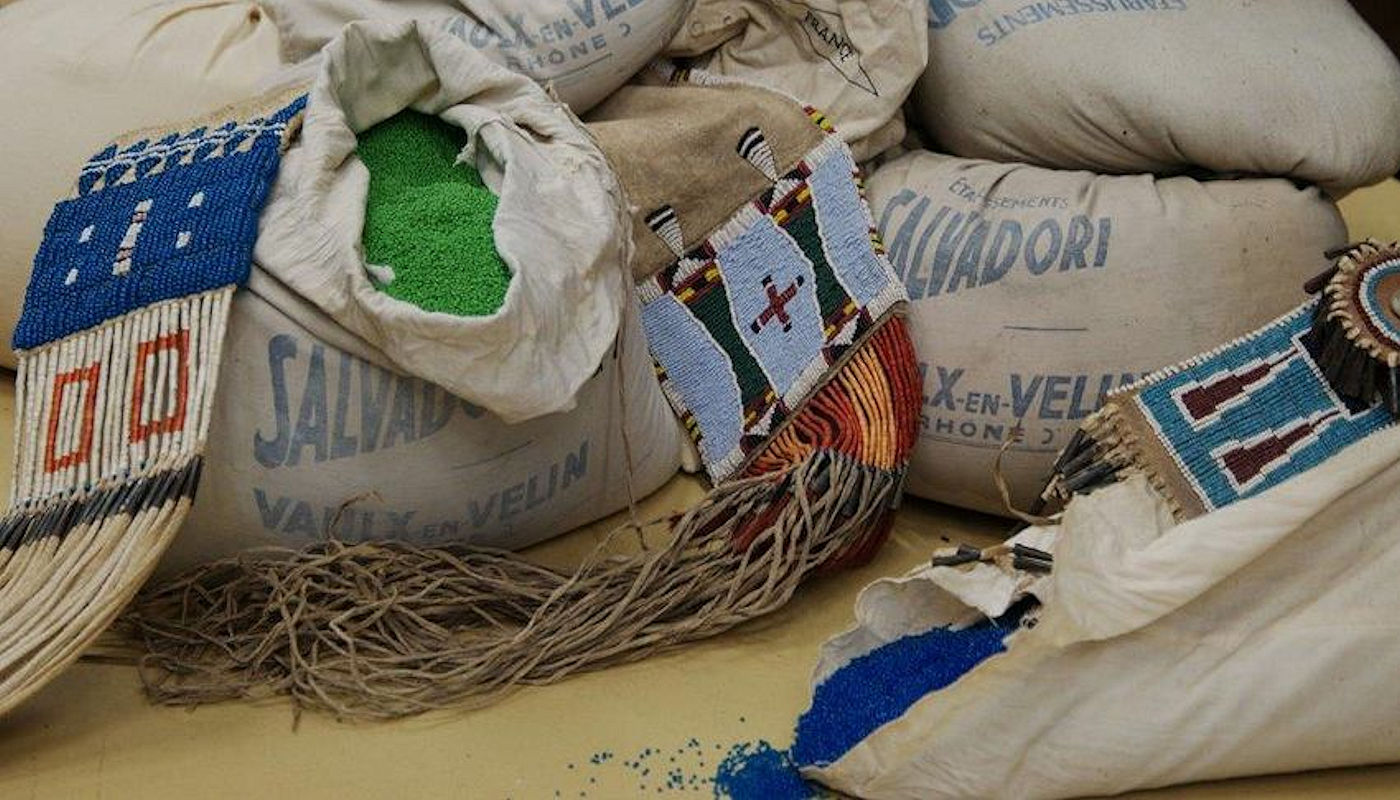
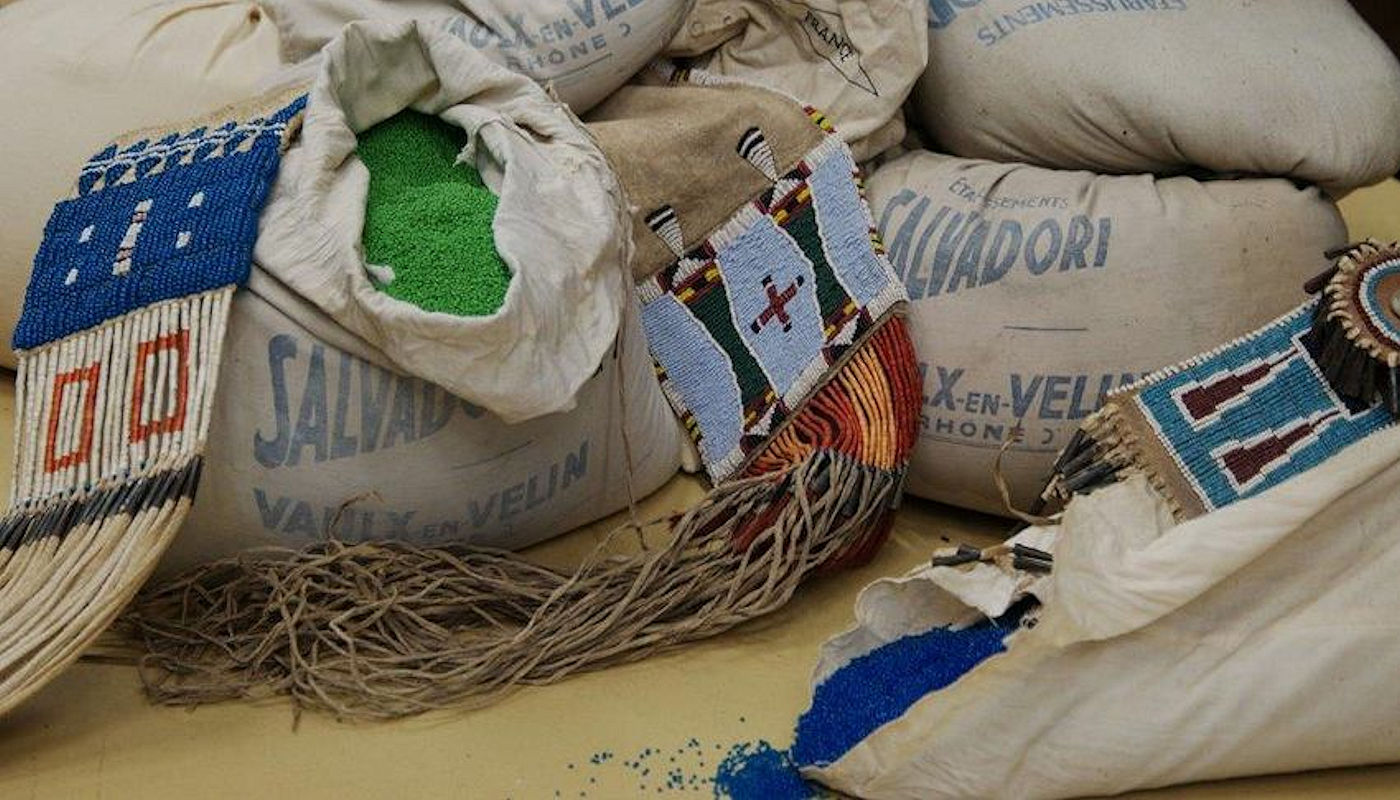
Czech Glass Seed Beads:
From European Glass Factories to Native American Material Culture
By Crazy Crow Trading Post ~ June 11, 2010
Czech Glass Seed Beads:
From European Glass Factories to Native American Material Culture
By Crazy Crow Trading Post ~ June 11, 2010
The purpose of this article on Czech Glass Seed Beads is to provide a thumbnail sketch of the history of one of the most popular trade items used in Native American craftwork. The use of the “seed bead” by Native Americans beginning in the 1800s was the result of hundreds of years of European glass technology intersecting with the westward expansion of the United States across the continent.
What is a Seed Bead?
The term seed bead is confusing as it is can refer to two different types of beads: beads made of nature’s seeds and beads produced in a factory. Obviously, our discussion is of glass seed beads produced in a factory.
Most seed beads are made of glass, however, other materials have been used such as those made of metal in France at the turn of the 19th century. Many of those metal beads were facetted.
Seed beads are made of drawn glass by literally drawing or pulling a hollow mass of glass into a long tube. This pulling can be done by one person alone, by two people or mechanically. The process looks like a taffy pull. The drawn glass tube is then cut into small pieces and then goes through several more processing steps in order to produce seed beads.
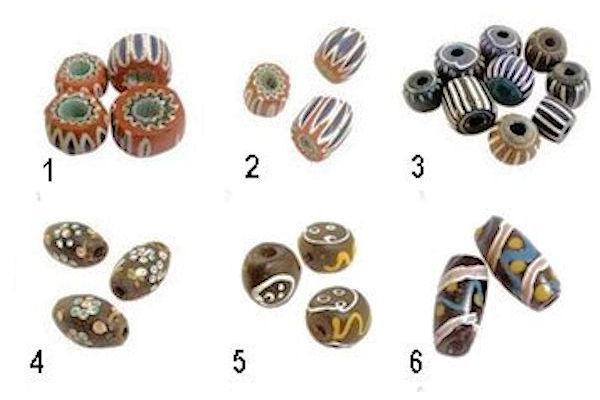

Trade Beads Through the Ages: 1. Seven Layer Chevron Bead. Late 1400s 2. Seven Layer Chevron Bead. Late 1400s 3. A Speo Bead. Late 1600s 4. French Ambassador Bead 1850s 5. Baule Face Bead. Late 1800s 6. Black Decorated Bead. Late 1800s 7. Cornaline D’Aleppo Bead. Late 1700s 8. Tabular Bead. Late 1800s 9. Large Chevron Bead. Late 1800s 10. Square Edge Floral Bead Late 1800s 11. Yellow Black Swirl Bird. Late 1800s 12. Millefiori Bead. Late 1800s
Venetian Glass Industry: Emergence of Glass Beads as a Global “Trade Currency” During Age of Discovery
The foundations for glass bead production in Venice were laid before 1500 AD. All glass production factories where moved to the island of Murano to protect the secrets of the Venetian glass making trade that was sought worldwide.
Venetian beadmakers used revolutionary glass making techniques for the time that greatly improved industrial production. This allowed them to overcome the earlier dominance of India and Far East Asia as competitors.
European glass-makers mass-produced huge quantities of beads from the 16th century through the 19th century during a period of exploration that extended to the corners of the earth. Most explorers, traders and missionaries carried glass beads with them as gifts or objects of barter to the native populations. European traders learned to identify local tastes in items used in personal adornment, and responded with appropriate choices to enhance their chances of success in their trade and travels.
A lively bead trade existed initially in most regions of Africa and beads made in Europe were then transported to West Africa by the European traders in their sailing ships, to be used as currency to purchase gold, ivory, palm oil and even slaves. Thus, the term “Trade Beads” typically applies to beads made predominately in Venice and Bohemia and, to a lesser extent, in other European countries from the late 1400s through to the early 1900s and traded in Africa and later in the Americas. This “trade” period peaked from the mid 1800s through to the early 1900s when literally millions of these beads were produced and traded.
Venetians dominated this market and produced the majority of the beads during this time. By the 18th Century, 44,000 pounds of Venetian glass beads were being produced each week and exported around the world. This came to an end following the campaign of Napoleon and the fall of the Republic of Venice.
This industry was considered indispensable, and for centuries they did everything they could to keep production techniques a secret. Severe penalties were used to prevent glass makers from leaving and setting up shop elsewhere. But monopolies do not last forever and many other countries worked to develop their own glass bead industries. The most successful of these was a forested and mountainous region of northern Bohemia, nowadays part of the Czech Republic.
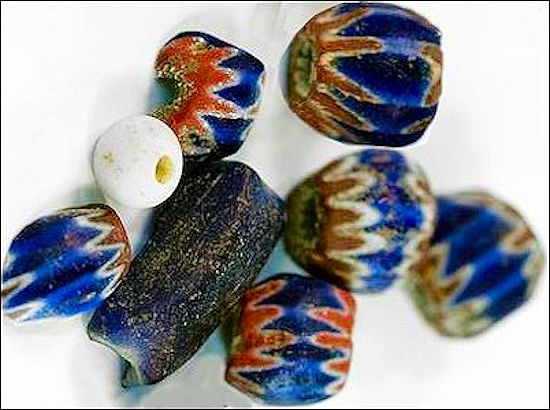
Tracking a conquistador with beads: DeSoto Identified by Chevron Beads in Georgia! Beads often reveal long-lost histories of countries, cultures, and people. For example, in November 2009, archaeologists with Atlanta’s Fernbank Museum of Natural History unearthed the first evidence of conquistador Hernando de Soto’s stay in Georgia, in the U.S., in 1540. The evidence used to make this determination is beads!
From European Glass Factories to Native American Material Culture
By the end of the 17th century, Czech glass factories had achieved worldwide recognition when the Czechs became masters in the art of pressed glass. Later, toward the end of the 19th century, seed beads became a major production item, making Czech glass beads the most popular choice for beading projects. Their popularity was due to a greater color selection, and much greater uniformity in size and shape from that of the earlier Italian seed beads. This craft started as a cottage industry with the forest glass makers, becoming more important as Czech glass seed beads became more popular as worldwide trade item, and today the art of crafting Czech glass seed beads is done in a factory.
Today the Czech Republic is in the forefront of the world bead market and Czech glass seed beads have been the best selling and most affordable with the broadest range of color, size and finish for over 50 years. Czech glass seed beads exhibit superior quality, outstanding uniformity, and exceptional breadth of assortment, making them the perfect choice for any beading project!
The most common shape for the Czech glass seed bead is like that of a donut, while the fire polished beads are generally round in shape. Fire polished beads are available in other shapes, too: bicone, rondelle, roller, roundlet, pear and parachute. Czech glass seed beads come in a variety of colors and this richness of color is one of the well known trademarks of Czech glass seed beads.
Crazy Crow Trading Post is one of the largest suppliers of Czech (and French) glass seed beads in the market today. They carry strung Czech glass seed beads rather than loose as they are better quality, more uniform in size and easier to use, with fewer culls. Crazy Crow Trading Post has a wide variety of opaque and transparent colored Czech glass seed beads to choose from which makes planning for your next beading project easier.
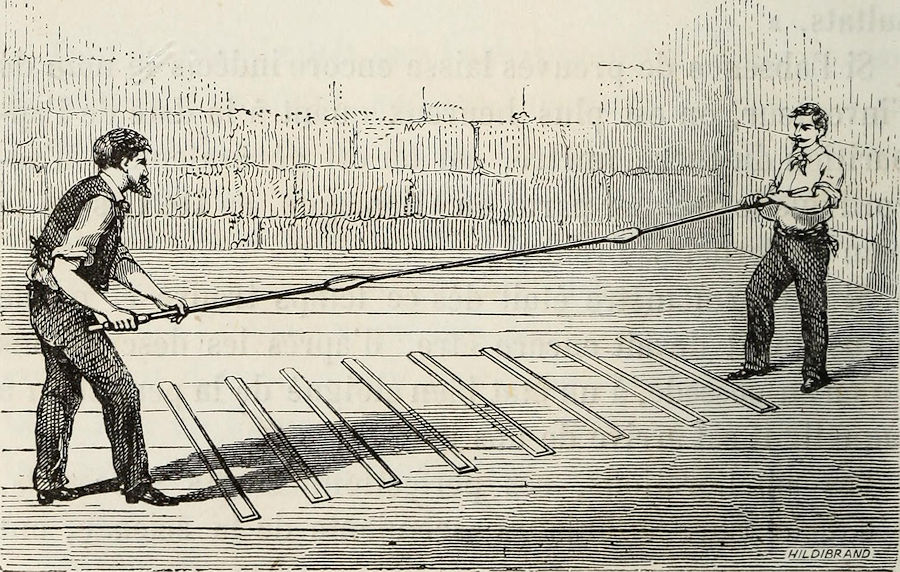
Credit Above Photo: Internet Archive Book Images, Drawing out of glass tubes for bead manufacture ca 1869. No restrictions, via Wikimedia Commons
Making of Czech Glass Seed Beads
Early Development of Czech Glass Industry
In the 1550s a major glass industry was founded in the cities of Jablonec, Stanovsko, and Bedrichov (modern Reichenberg) in Bohemia (in the current Czech Republic). Glassmakers there were mostly cottage crafters making products for larger centralized factories. This region became the center of this industry because it provided the material and manpower needed for it to thrive.
First, nearby mountains contained quartz deposits that were easily mined. Second, Bohemia had an abundance of cheap skilled labor. Third, and most important, the forests provided an abundant source for wood to heat the large furnaces required to melt glass. The forests also provided an essential by-product that was needed, potash, which resulted from burning wood in the furnaces. Importing this potash, an important ingredient in glass making, would have been very expensive. It takes between 15,000 and 40,000 pounds of wood to create the potash to make 50 pounds of Czech glass. The wood burned in the furnaces created the ash that was later collected to make all the potash that was needed. These Bohemian factories turned out mainly glassware and cut glass stones. Beads were a secondary product.
Important Bead Manufacturing Technology Advances of 1860
The original seed beads were made in Italy from round tubes producing round seed beads. For years the Italians held the monopoly on the process. The Czechs entered the marketplace in the late 18th century.
From earliest times there have been many ways of forming glass beads. The earliest was to wind molten glass around a form and allow it to set and cool, creating round beads. The glass can also be blown into a form or mold, creating hollow shapes in the beads which are lighter than wound ones. A third method is to create blown glass beads without a mold. Beads made in this way are the lightest and most delicate. All these methods have been known for thousands of years, but it was not until 1860 that the first pressed glass molds were developed in Bohemia, producing a product that is more durable and robust than earlier methods.
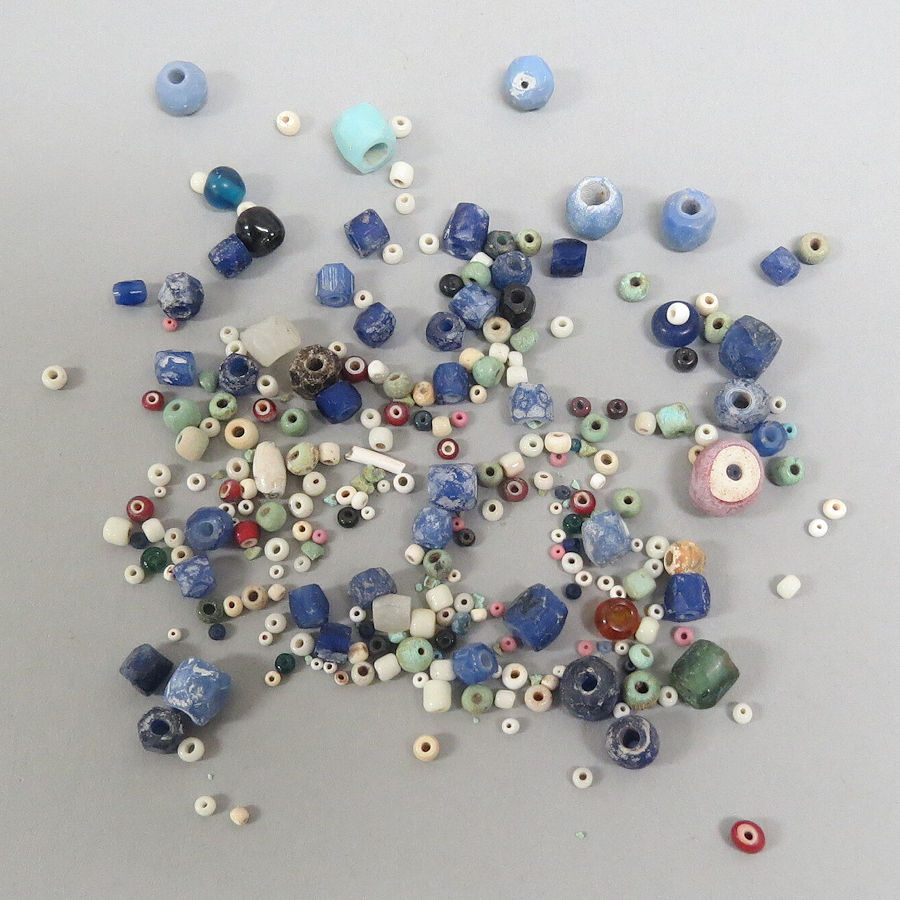
Credit Above Photo: English: NPS Photo, Public domain, via Wikimedia Commons
Some claim that the production of drawn beads in the early 18th century was the most important development in the history of beads. It was the first time that beads did not have to be individually hand made. Instead, beads could simply be cut en masse from tubes of drawn glass. Mass production had arrived in bead making. In the 1860s several new processes and machines were developed which enabled bead makers to achieve uniformity of colors and sizes in seed beads. But perhaps the biggest boon to seed beads came in the early 20th century when a machine was made to automatically draw glass tubes.
‘Pressing’ was a completely new process. A dollop of glass was taken up and placed in a pair of mold tongs, after it was formed it would be pierced by an iron rod. The bead was then drawn off the rod and allowed to cool slowly. This method left a wide seam around the circumference of the bead, which would be ground away after the bead cooled.
Later this process became automated by hydraulic bead presses which could turn out thousands of identical beads quickly. The presses used a combination of high pressure and heat caused by that pressure to convert powdered glass into glass beads. After the beads were formed they were pierced using high speed drills to create uniform holes. Pressed glass beads are denser than other types and the fact that the beads are pierced after they are formed means that offset or multiple holes are possible. The creative possibilities are endless.
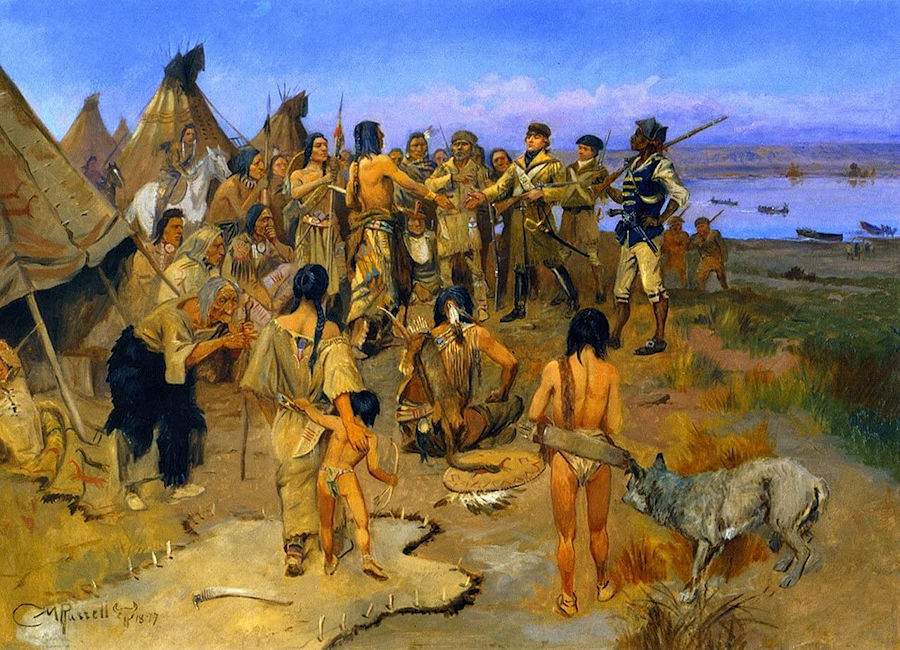
Credit Above Photo: Charles Marion Russell Painting: Lewis and Clark meeting the Mandan., Public domain, via Wikimedia Commons
Historic Timeline of Glass Beads
Roman Times: People were making glass beads in Bohemia, in the present-day Czech Republic, as early as 250 B.C. In the 900s (A.D.), handmade beads were placed in graves.
Middle Ages: During the 13th century, people began moving into the area’s northern mountains and opened several glass factories. Resources such as laborers, water and wood for furnaces helped supply the factories.
Years 1500-1800: A cottage industry began in the Bohemian cities of Jablonec, Stanovsko and Bedrichov in the 1500s. These glassmakers made beads for larger jewelry factories.
Mid-1800s: Czech “sample men” traveled the world, taking notes and sketches of the various kinds of beads people wanted. Back home, the factories made these new designs, which sold well and in turn increased the demand for beads.
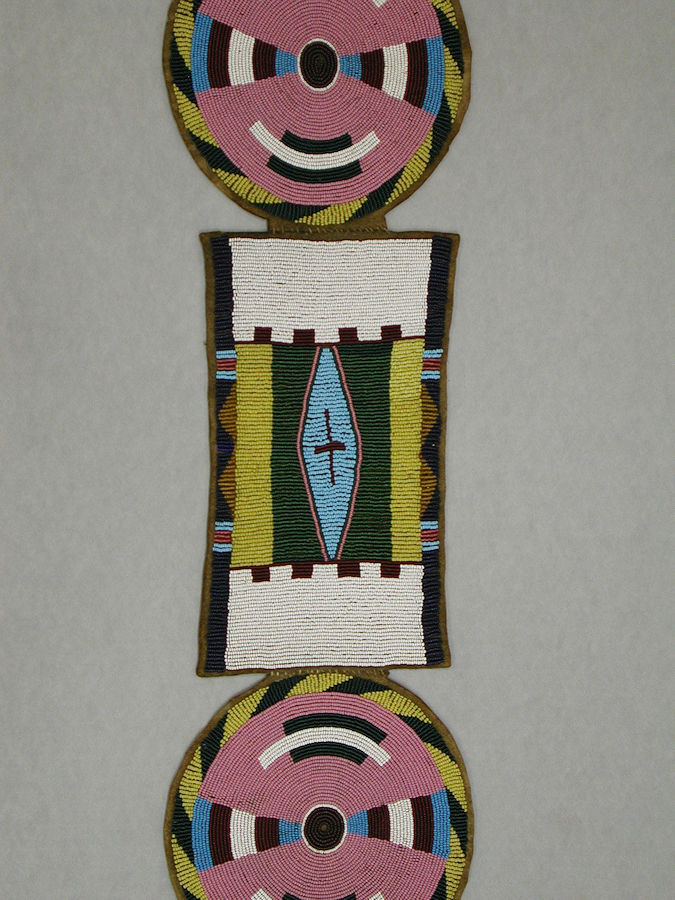
Credit Above Photo: Crow Blanket strip ca 1875 – Metropolitan Museum of Art, CC0, via Wikimedia Commons
Late 1800s: Technological advances, like multi-bead molds and machines to handle some of this work, made Bohemia a center for pressed-glass beads.
1920s: Czechs became leading bead exporters in the world.
The Czech bead industry has had its ups and downs since, due to economic conditions, wars, and politics, but Czech glass beads remain one of the most important elements in the jewelry-maker’s tool kit.
Today: Czech bead-making suffered setbacks because of two world wars, the Great Depression and Communist rule. Anyone trying to buy cut seed beads while it was a communist country know that the difference between then and now as to the availability of colors. If you were lucky in those days, there might be five colors available in a year, and one was always black.
Since the fall of communism, the industry has been revived, driven by demand rather than central planning, and Czech bead makers are again among the world leaders in bead manufacturing and exports.
Popularity of Seed Beads
Seed beads were immediately popular. They were used as decoration on clothes and other items. In many cases, the seed beads allowed people to enhance their outfits much more elaborately than had previously been possible. North American Indians used the seed beads acquired through trade to embellish clothing and many articles of everyday and ceremonial life. Until their introduction, these Native American tribes had mainly used shells and dyed porcupine quills for adornment.
Typical Native American Tribal Bead Color Preferences
The use of colors by Indian beadworkers varies widely among the many different tribes throughout the U.S. & Canada. These are general guidelines for some of the better known beadworking tribes. Many exceptions to this can be found, but this provides a basis for staying within the traditions for these tribes. One should also be aware that many variations of hues existed within given shades of colors, and these varied from factory to factory as well as in different lots from the same factory.
See color chart by tribe and article on Native American Tribal Color Preference.
Crazy Crow Articles
Current Crow Calls Sale
July – August
SAVE 10%-25% on popular powwow, rendezvous, historic reenactor, bead & leather crafter supplies. It’s official, Summer is here, and so is the heart of Powwow, Rendezvous & Historic Reenactment seasons. 4th of July Celebrations is here, and just blink and Labor Day will be here. This sale offers many popular items for Native American, Rendezvous & Historic Reenactment outfits. Sale items include our Missouri River Brand Serape Blankets, a big DVD sale, Missouri River Patterns, 18th Century Linen Hunting Shirts, select Damascus Knives, Buckskin Splits, Bone & Horn Hairpipe, Plastic Crow Beads, Leather Pouches & Bags, and much more!